شمش روی نوعی فلز با ارزش است که از طریق فرآیندی به نام استخراج و ذوب سنگ معدن روی به دست میآید. این فلز کاربردهای مختلفی در صنایع مختلف از جمله گالوانیزه کردن، ساخت باتری، و تولید آلیاژها دارد.
روی (Zinc) یکی از فلزات مهم صنعتی است که استفاده از آن به چند هزار سال قبل بازمیگردد. اولین استفادهها از روی در آلیاژ برنج (مخلوط مس و روی) در دوران باستان بوده است. از قرن نوزدهم میلادی، استخراج و تولید روی به روشهای مدرنتر انجام شد و به عنوان یک فلز خالص مورد استفاده قرار گرفت.
خرید مواد و تجهیزات استخراج
برای خرید آنلاین مواد و تجهیزات استخراج با بهترین قیمت و تضمین کیفیت از بهترین برندهای موجود بازار از فروشگاه معتبر ایآز بازدید نمائید.
فهرست مطالب مقاله
یکی از فرآورده های بسیار مهم و ارزشمند فلز روی، شمش روی است. شمش روی از قابلیت های ویژه ای برخوردار است که مهم ترین آن دوام و مقاومت بالای این محصول در برابر خوردگی است. این ویژگی منحصر به فرد در شمش روی باعث شده تا بتوان از آن در صنایع مختلف برای عملیات گالوانیزاسیون محصولات استفاده شود.کاربردهای این محصول در صنایع مختلفی همچون صنعت پزشکی، تولید قطعات الکتریکی، صنایع ریخته گری و… به وضوح نمایان است،
معرفی فلز روی
فلز روی که آن را با نماد شیمیایی Zn نشان می دهند، فلزی است شکننده که با رنگ های ترکیبی آبی و نقره ای در طبیعت یافت می شود. از نظر فراوانی فلز روی جزء بیست و چهارمین عناصر موجود در طبیعت است که می توان آن را از سنگ معدن اسفالریت استخراج کرد. فلز روی اصولا دارای یک سری ویژگی ها و مشخصات فیزیکی و شیمیایی است که آن را نسبت به برخی فلزات دیگر متمایز کرده است.

از جمله این ویژگی ها می توان به خاصیت الکتروشیمیایی بودن روی، شکل پذیری قابل قبول، دوام در برابر خوردگی، نقطه ذوب پایین، سختی و مقاومت کافی، سیالیت و…اشاره کرد. فلز روی آنچنان ارزشمند و مهم است که از آن آلیاژهای مختلفی را نیز تولید و روانه بازار می کنند. این امکان تولید آلیاژهای مختلف از فلز روی نیز یکی دیگر از قابلیت های آن است. شمش روی از جمله محصولات این فلز است که تمامی قابلیت های فلز روی را در خود داراست.
تاریخچه فلز روی
استفاده از روی به تمدنهای باستانی مصر و هند بازمیگردد. در هند حدود 2000 سال پیش ، روی به عنوان فلز خالص استخراج میشد. یونانیها و رومیها از آلیاژ برنج (مس و روی) برای ساخت سکهها و وسایل تزئینی استفاده میکردند.
استخراج و استفاده از روی در اروپا، خاورمیانه، و چین پیشرفت کرد. کیمیاگران مسلمان و دانشمندان چینی به استفاده از روی اشاره کردهاند. در سال 1746، آندریاس زیگسموند مارگراف، فرآیند استخراج روی خالص را توسعه داد. تولید صنعتی روی در اروپا آغاز شد.
استفاده گسترده از روی در صنایع مختلف بهویژه گالوانیزه کردن آهن و فولاد. تولید روی در مقیاس بزرگ صنعتی انجام شد و به عنوان فلزی استراتژیک در صنایع نظامی و غیرنظامی مورد استفاده قرار گرفت. تکنیکهای مدرن استخراج و فرآوری باعث افزایش بازدهی و کاهش هزینههای تولید شدهاند.
منابع و معادن استخراج فلز روی
فلز روی یکی از منابع معدنی مهم در سطح جهان است و استخراج آن از معادن گوناگون انجام میشود. منابع و معادن روی در سراسر جهان پراکندهاند، اما برخی از مهمترین آنها در نقاط زیر قرار دارند:
منابع اصلی فلز روی
- اسفالریت (Sphalerite): اصلیترین سنگ معدن روی که حاوی سولفید روی (ZnS) است.
- اسمیتزونیت (Smithsonite): حاوی کربنات روی (ZnCO₃).
- همیمورفیت (Hemimorphite): حاوی سیلیکات روی (Zn₄Si₂O₇(OH)₂·H₂O).
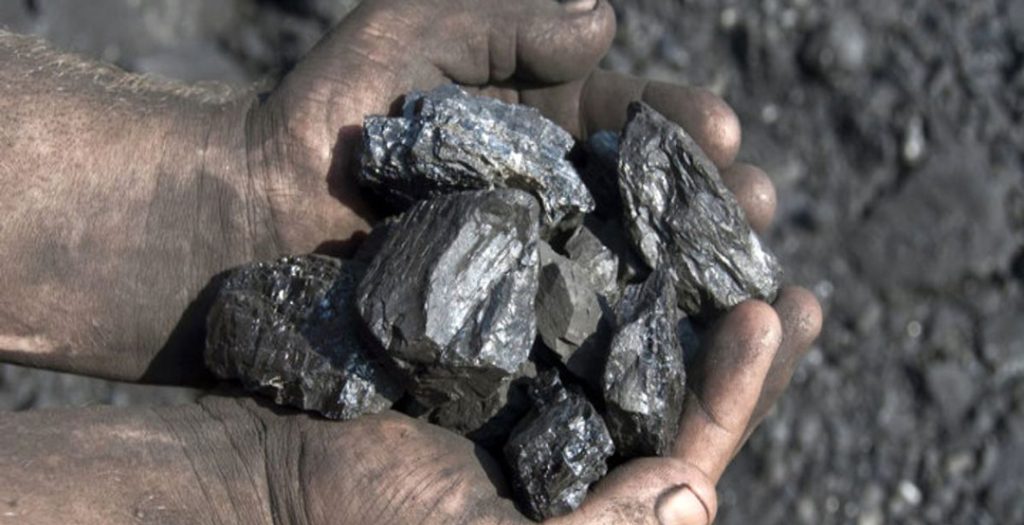
معادن بزرگ روی در جهان
استرالیا:
- معدن مونت آیزا (Mount Isa): در کوئینزلند، یکی از بزرگترین معادن روی جهان.
- معدن بروکن هیل (Broken Hill): در نیو ساوت ولز، از قدیمیترین و بزرگترین معادن روی.
چین:
- معدن هونان (Hunan): از بزرگترین تولیدکنندگان روی در چین.
- معدن هولوداو (Huludao): در شمال شرقی چین، معدن مهم روی.
کانادا:
- معدن رد داگ (Red Dog): در آلاسکا، بزرگترین معدن روی جهان از نظر تولید سالانه.
- معدن سنت کلود (Saint Cloud): در کبک، معدن مهم روی کانادا.
پرو:
- معدن آنتامینا (Antamina): در آندها، یکی از بزرگترین معادن روی و مس جهان.
- معدن سرو (Cerro de Pasco): دیگر معدن مهم روی در پرو.
آمریکا:
- معدن تریل (Trail): در بریتیش کلمبیا، بزرگترین تولیدکننده روی در آمریکای شمالی.
- معدن ایمپریال اسمتلتر (Imperial Smelter): در ایلینوی، معدن مهم روی آمریکا.
این معادن و منابع، پایه اصلی تولید فلز روی در جهان هستند و تأمینکننده نیازهای صنایع مختلف به این فلز ارزشمند میباشند.
روش های استخراج فلز روی
استخراج فلز روی شامل مراحل مختلفی است که به دو روش اصلی تقسیم میشود: روش پیرومتالورژی (حرارتی) و روش هیدرومتالورژی (تر). هر یک از این روشها به مراحل و فرآیندهای خاصی نیاز دارند.

1. پیرومتالورژی (Pyrometallurgy)
- آمادهسازی سنگ معدن: خرد کردن و آسیاب کردن سنگ معدن.
- تشویه: حرارت دادن سنگ معدن در دماهای بالا برای تبدیل سولفید روی به اکسید روی.
- احیا: احیا کردن اکسید روی با کربن یا مونوکسید کربن برای تولید فلز روی.
- تقطیر: تقطیر روی مذاب برای جدا کردن فلز خالص.
2. هیدرومتالورژی (Hydrometallurgy)
- لیچینگ: حل کردن سنگ معدن در محلول اسید سولفوریک برای تولید سولفات روی.
- خالصسازی: رسوب دادن ناخالصیها از محلول سولفات روی.
- الکترولیز: رسوب دادن فلز روی در کاتد از محلول خالص شده.
- ذوب و ریختهگری: ذوب کردن روی استخراج شده و ریختهگری آن به شکل شمش.
مراحل کلی تولید شمش روی
تولید شمش روی شامل چندین مرحله از استخراج سنگ معدن تا فرآوری نهایی و ریختهگری است. این مراحل به طور خلاصه به صورت زیر میباشد:
1. استخراج سنگ معدن
- سنگهای حاوی روی مانند اسفالریت (ZnS) از معادن روباز یا زیرزمینی استخراج میشوند.
2. آمادهسازی سنگ معدن
- سنگ معدن استخراج شده خرد و آسیاب میشود تا به ذرات ریز تبدیل شود و آماده فرآوری گردد.
3. فرآیند تشویه (Roasting)
- سنگ معدن خرد شده در کورههای تشویه حرارت داده میشود تا سولفید روی (ZnS) به اکسید روی (ZnO) تبدیل شود. در این فرآیند گوگرد به صورت گاز دیاکسید گوگرد (SO2) آزاد میشود.
4. لیچینگ (Leaching)
- اکسید روی (ZnO) در محلول اسید سولفوریک حل میشود تا سولفات روی (ZnSO4) تشکیل شود.
5. خالصسازی محلول (Purification)
- محلول حاوی سولفات روی از ناخالصیها پاکسازی میشود. این کار با افزودن مواد شیمیایی مختلف انجام میشود که ناخالصیها را رسوب میدهند.
6. الکترولیز (Electrolysis)
- محلول خالص سولفات روی به سلولهای الکترولیز منتقل میشود. در این سلولها، جریان الکتریکی باعث رسوب فلز روی بر روی کاتد و تولید گاز اکسیژن در آند میشود.

7. ذوب و ریختهگری (Melting and Casting)
- فلز روی که در فرآیند الکترولیز به دست آمده است، در کورههای خاصی ذوب میشود.
- روی مذاب به داخل قالبهای مخصوص ریخته میشود تا پس از سرد شدن به شکل شمش درآید.
نکات اضافی
- کنترل کیفیت: در طول مراحل مختلف، آزمایشات کیفی برای اطمینان از خلوص و کیفیت فلز روی انجام میشود.
- بازیافت: برخی از کارخانهها ضایعات و مواد جانبی تولید شده را بازیافت کرده و به چرخه تولید بازمیگردانند.
عوامل موثر بر کیفیت شمش روی
کیفیت شمش روی به عوامل مختلفی بستگی دارد که میتوان آنها را به دو دسته کلی عوامل مربوط به سنگ معدن و عوامل مربوط به فرآیند تولید تقسیم کرد.
عوامل مربوط به سنگ معدن:
- عیار سنگ معدن: عیار سنگ معدن به معنای درصد خالص بودن سولفید روی (ZnS) در آن است. هر چه عیار سنگ معدن بالاتر باشد، کیفیت شمش روی تولیدی نیز بهتر خواهد بود.
- ناخالصیهای موجود در سنگ معدن: وجود ناخالصیهایی مانند سرب، آهن، کادمیم و آرسنیک در سنگ معدن میتواند کیفیت شمش روی را به طور قابل توجهی کاهش دهد.
- نوع و پراکندگی کانیهای موجود در سنگ معدن: نوع و پراکندگی کانیهای موجود در سنگ معدن میتواند بر فرآیند استخراج و فرآوری آن تاثیر بگذارد و به طور غیرمستقیم بر کیفیت شمش روی تولیدی اثرگذار باشد.
عوامل مربوط به فرآیند تولید:
- روشهای استخراج و فرآوری سنگ معدن: روشهای مختلفی برای استخراج و فرآوری سنگ معدن روی وجود دارد که هر کدام مزایا و معایب خاص خود را دارند. انتخاب روش مناسب استخراج و فرآوری میتواند به طور قابل توجهی بر کیفیت شمش روی تولیدی تاثیر بگذارد.
- تکنولوژی و تجهیزات مورد استفاده در کارخانههای فرآوری: استفاده از تکنولوژی و تجهیزات مدرن و پیشرفته میتواند به افزایش کیفیت شمش روی تولیدی کمک کند.
- مهارت و تجربه اپراتورها: مهارت و تجربه اپراتورهای کارخانههای فرآوری نیز میتواند بر کیفیت شمش روی تولیدی تاثیرگذار باشد.
- کنترل کیفیت در مراحل مختلف تولید: انجام کنترل کیفیت در مراحل مختلف تولید شمش روی از جمله استخراج، کنسانتره سازی، کلسیناسیون، احیا و ذوب میتواند به شناسایی و رفع عیوب احتمالی و در نهایت به افزایش کیفیت شمش روی تولیدی کمک کند.